1. Thermoplastics
Thermoplastics are the most commonly used materials in injection molding due to their versatility and wide range of properties. These materials have the ability to soften when heated and solidify upon cooling repeatedly, allowing for easy molding and recycling processes. Some of the popular thermoplastics used in injection molding include:
Polypropylene (PP)
Polypropylene is a lightweight and flexible thermoplastic that offers excellent chemical resistance, low cost, and high impact strength. It is commonly used in the automotive, packaging, and consumer goods industries.
Acrylonitrile Butadiene Styrene (ABS)
ABS is a strong and durable thermoplastic that possesses good impact resistance and dimensional stability. It is often used in the production of electronic enclosures, automotive components, and household appliances.
Polycarbonate (PC)
Polycarbonate is a transparent and highly impact-resistant thermoplastic. It is known for its excellent optical clarity, making it suitable for applications such as safety goggles, lenses, and automotive lighting.
Polyethylene (PE)
Polyethylene is a versatile thermoplastic that comes in various forms, including high-density polyethylene (HDPE) and low-density polyethylene (LDPE). It offers excellent chemical resistance, electrical insulation properties, and is commonly used in packaging and piping systems.
2. Engineering Plastics
Engineering plastics are a class of materials that exhibit enhanced mechanical, thermal, and chemical properties compared to standard thermoplastics. These materials are specifically designed to withstand demanding environments and provide superior performance. Here are some notable examples:
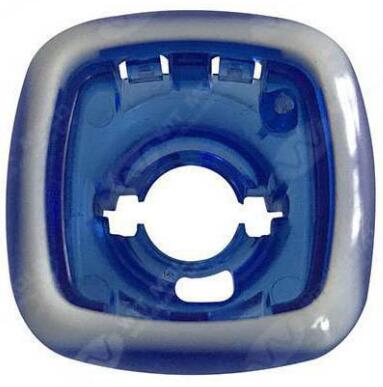
Polyamide (PA)
Polyamide, commonly known as nylon, is a strong and lightweight engineering plastic. It possesses excellent tensile strength, abrasion resistance, and is often utilized in applications such as gears, bearings, and structural components.
Polycarbonate-ABS (PC-ABS)
PC-ABS is a blend of polycarbonate and ABS, combining the toughness and heat resistance of polycarbonate with the processability and cost-effectiveness of ABS. It finds extensive use in automotive, electronics, and telecommunications industries.
Polyether Ether Ketone (PEEK)
PEEK is a high-performance engineering plastic known for its exceptional mechanical, thermal, and chemical resistance properties. It is commonly employed in aerospace, medical, and oil and gas applications where extreme conditions are present.
Polyphenylene Sulfide (PPS)
PPS is a high-temperature engineering plastic that offers excellent chemical resistance and dimensional stability at elevated temperatures. It is often used in electrical and electronic components, as well as automotive parts.
3. Elastomers
Elastomers, also known as rubber-like materials, are characterized by their elasticity and flexibility. They are commonly utilized when parts require excellent sealing, cushioning, or shock-absorbing properties. Let’s explore a few examples:
Thermoplastic Elastomers (TPE)
TPEs are a versatile group of elastomers that combine the processing advantages of thermoplastics with the elasticity and softness of traditional rubber. They find extensive use in the automotive industry, medical devices, and consumer products.
Silicone
Silicone elastomers are known for their high-temperature resistance, low toxicity, and excellent electrical insulation properties. They are widely used in the medical and food industries, as well as for seals, gaskets, and electronic components.
Conclusion
In summary, the materials used for injection molding are diverse and tailored to meet specific requirements in terms of strength, flexibility, chemical resistance, and more. This article provided an overview of various materials, including thermoplastics like polypropylene, ABS, polycarbonate, and polyethylene, as well as engineering plastics such as polyamide, PC-ABS, PEEK, and PPS. Additionally, elastomers like TPEs and silicone were also discussed. By understanding the unique properties of these materials, you can make informed decisions and select the most suitable option for your injection molding needs.
Remember, choosing the right material is crucial in achieving high-quality and cost-effective production. Always consult with experts in the field to ensure the optimal selection of materials for your specific application. WIT MOLD can meet the demand for plastic products that are reasonably priced, durable, and require precise specifications every time. We are your one-stop supplier of high-quality, cost-competitive domestic molded plastic products using various plastic materials.
没有评论:
发表评论